Ion exchange (IX) is one of the most cost-effective and reliable water quality improvement technologies in the marketplace today; proving itself year-over-year as the gold standard for cost, performance, and dependability.
Ion exchange technology can be used in residential, commercial, and industrial processing applications to soften, condition, and even purify potable and graywater water.
As with many advanced technologies, ion exchange is often easy to deploy at the entry-level, even though there is much more to it than most dealers realize. Entry-level applications include traditional salt-based softening and nitrate removal applications, but there is so much more that you can do and there are great strides in operational efficiency and effectiveness to be achieved if you’re willing to take the time and effort to learn more about ion-exchange technology.
The key to understanding Ion Exchange is to emphasize the actual “exchange” process, where one ion is exchanged for another with the resulting byproduct/s of exchange remaining in the treated water-stream. This exchange is the key to understanding how IX can be incorporated into your portfolio.
In the February 2013 issue of WC&P we introduced you to the basics of Ion Exchange, so I will not bore you by repeating it. We will also not discuss demineralization in this article, since that requires an article all of its own. Instead, we’ll dive right in to expanding the repertoire with some more esoteric applications…
Aqueous metallic ions are positively charged (cations), and non-metallic ions are usually negatively charged (anions). Selection of resin for treatment as well as the operating performance of that resin depends on the concentration of contaminants in the water as well as the resin’s relative affinity for the contaminants and their interfering factors. Strong Acid Cation (SAC) resin is generally recognized as the most popular resin in use today.
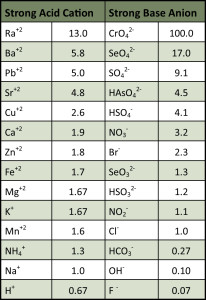
As you can see in Table 1, a typical Strong Acid Cation (SAC) Resin is highly attracted to heavy metals, and less so to the “regenerant ions” (sodium and hydrogen), which is why we can deploy SAC so effectively in highly sodic waters and still be able to remove calcium (albeit with some ionic leakage). The resin’s affinity varies with the ionic size and charge of the aqueous ion, generally favoring large, highly charged ions. Refer to figure 1. for a representation of the functional group in this type of resin.
Naturally, during regeneration a less attractive ion like sodium or hydrogen is used to regenerate the resin and the only way it can force the entrained ions off of the resin’s functional groups is due to being in a highly concentrated form. This phenomenon is referred to as “mass action”. From a design perspective, we need to consider mass action carefully when calculating brine/rinse rates on high hardness waters and deciding on the injection system design, since drawing the brine solution through the resin bed too slowly can actually result in reversal of the regeneration reaction and cause contaminants to be driven back into the resin media. I see this quite frequently where dealers try to cut corners by using undersized equipment on water with high hardness, high Total Dissolved Solids (TDS), or where there are significant amounts of other interfering metallic ions in the water.
When working on wastewater applications, SAC resin is used to great effect in removing regulated contaminants like copper and zinc, but if the dealer doesn’t understand the overall holistic of the application their efforts might be stymied by something as simple as the inclusion of water softener regenerant waste in the discharge stream to be treated. By including the highly concentrated solution of calcium ions in the stream, it makes the resin’s task of removing the copper and zinc significantly more difficult, and sometimes absolutely impossible. Always remember to fully understand your process before diving in and recommending solutions.
Weak Acid Cation (WAC) resin has a high selectivity for divalent cations such as copper and nickel (especially at neutral to alkaline pH levels), so it is naturally an excellent choice in wastewater applications as a cost-efficient alternative to chelating resins. WAC resins have the highest capacity of any IX material in the general marketplace at the time of this writing which makes it ideal for deployment in conjunction with an SAC resin to maximize performance and cost-efficiency. This high capacity naturally means that it both shrinks and swells significantly under various conditions of operation, so exercise appropriate caution if you decide to mix SAC and WAC in the same tank. Refer to Figure 4 to see the functional group for this type of resin.
Referring back to Table 1, we see the relative affinity of Strong Base Anion (SBA) resin, which is the second-most popular resin used by dealers in the United States. Refer to figure 2. for the functional group contained in this type of resin.
Many dealers have used SBA resin to address sulfates, nitrates, and silicates in water, but I see all too often that the rationale for use and an understanding of complicating factors in the water are usually grossly misunderstood. Unless specifically engineered to be selective for one anion over others, SBA resins are attracted to all of the “-ates” in descending order by their molecular size and valence charge. The most frequent faux pas that I see is using SBA for Nitrate removal in sulfate-bearing waters and having the sulfate concentration overwhelm the nitrate-laden resin as it becomes exhausted and then causing “dumping” of nitrates back into the water. It is crucially important to always test for sulfates, and silicates when attempting to address nitrates in water. This will enable you to calculate the true capacity of the resin during service, instead of merely its capacity for the one thing that you’re wanting to treat.
SBA can also be used as an excellent organic scavenger for wastewater or industrial process applications. Modern purpose-built Macroporous SBA resins are highly effective at removing tannins from water and I encourage dealers to use “tannin selective” resins when dealing with colored water issues involving Natural organic materials, such as fulvic or humic acid compounds. Remember again that even though you’re addressing tannins, your SBA IX resin is attracted to other contaminants in the water and you should test for them as well to ensure your system is going to work as expected.
Type 2 SBA Resin is less selective for general anions and employed primarily in dealkalization applications while operating in the chloride form. Many low pressure boilers worldwide are being effectively protected by the combination of a sodium softener and chloride dealkalizer. A properly designed anion dealkalizer will typically remove 90-95% of the carbonate (CO32-) and bicarbonate (HCO3–) alkalinity as well as 99% of the sulfates (SO42-) and nitrates (NO3–). A dealkalizer will yield substantially higher capacity when regenerated with both salt and caustic soda. Refer to figure 3 to see its typical functional group.
A lot of dealers try to “value engineer” by deploying anion IX equipment as the sole treatment technology. This is rarely an appropriate choice and will inevitable result in other issues later that cost the dealer customer satisfaction and callback costs. The ideal situation is to always soften upstream of anion media to minimize complications during service and regeneration.
Mixing anion and cation resin in the same tank can be a subject of much emotion and controversy to some dealers since it is used as a selling-point by some. My personal rule is that I will only mix media if the influent hardness level is below 8 gpg (137 mg/l), since the risk of fouling with calcium carbonate and calcium sulfate compounds becomes too high. Also remember that anion resin is much less dense than cation resin and a top distributor screen should always be used to prevent resin loss during backwash.
There’s a big world of Ion Exchange applications out there, just waiting for you to explore. Talk to your OEM, or dealer network to learn more about how ion exchange technology can enrich your dealership and provide valuable solutions to your client base.
Figure 1: Strong Acid Cation (SAC) Functional Group
Figure 2: Type 1 Strong Base Anion (SBA) Functional Group
Figure 3: Type 2 Strong Base Anion (SBA) Functional Group
Figure 4: Weak Acid Cation (WAC) Functional Group
Image Credit: Images courtesy of C.F. ‘Chubb’ Michaud and the Innovative Water Project.